Ecofelt
for non-woven
with a positive impact
The quality of our production does not stop at just the physical and technical performance of non-woven fabrics. We strive daily to make our fabrics as virtuous as possible. That way, they can be incorporated into your projects with a genuinely positive impact for the environment and for the health of those using your products.
It is from this major concern that Ecofelt was born. Our non-woven fabrics, derived from circular economy systems, bio-sourced, recyclable, or compostable, are composed of at least 50% regenerated fibres (PET, BICO, VIS), post-consumer fibres (aramid, polyester), production waste (colour transitions, second choice, grade B), organic or agriculturally sourced fibres (natural: cotton, linen, hemp or artificial: viscose).
Today, 50% of our production meets this requirement. Our Research & Development and Production teams are committed to combining performance with care, in every circumstance.
Guaranteeing high standards of product quality and performance is an absolute imperative for us. To achieve this, we meticulously consider, study, test, and monitor the use of our production waste as raw material. In 2022, our expertise enabled us to internally upcycle twice as much material as in the previous year.
Research & Development
Eco-design is central to all our considerations and decisions, as is the search for solutions that allow you to have a positive impact on the environment and the well-being of all. These are the forces that drive our progress. Our Ecofelt product range already includes several products made from 100% recycled fibres.
Each new project is an opportunity to re-examine the entire chain, from sourcing through production to delivery, while consistently guaranteeing high standards of performance and durability for our non-woven fabrics.
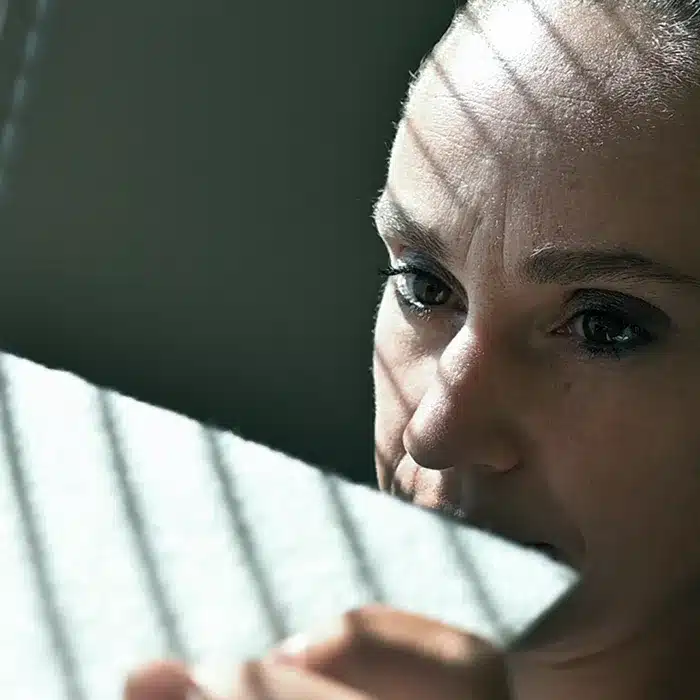
Purchasing / Resources
The purchasing sector for raw materials from recycling is constantly evolving. The performance of such materials, which have become as valuable as they are virtuous, is now recognised and accepted.
The engineers at our laboratory are constantly seeking new solutions and combinations of materials, testing them, and implementing them, to make sure we achieve the expected performance in all circumstances while preserving each resource.
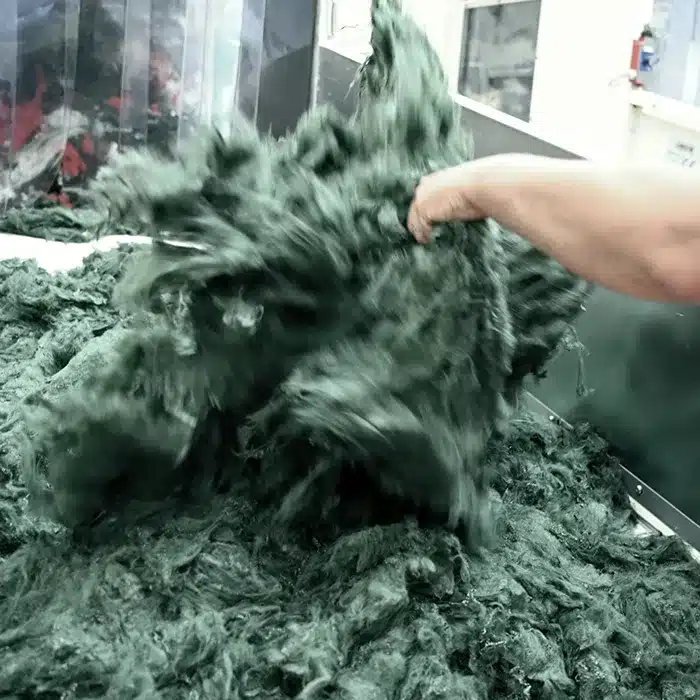
Production
Over the past two years, Duflot has reduced its electricity needs by 12%. What made these reductions possible was the ingenuity and adequacy of the solutions created by our R&D team, along the accumulation of (small) daily actions taken by each employee, that, all together, make Duflot a responsible company.
Material recovery bins have appeared beside the machines. Using them is part of the company’s best practices.
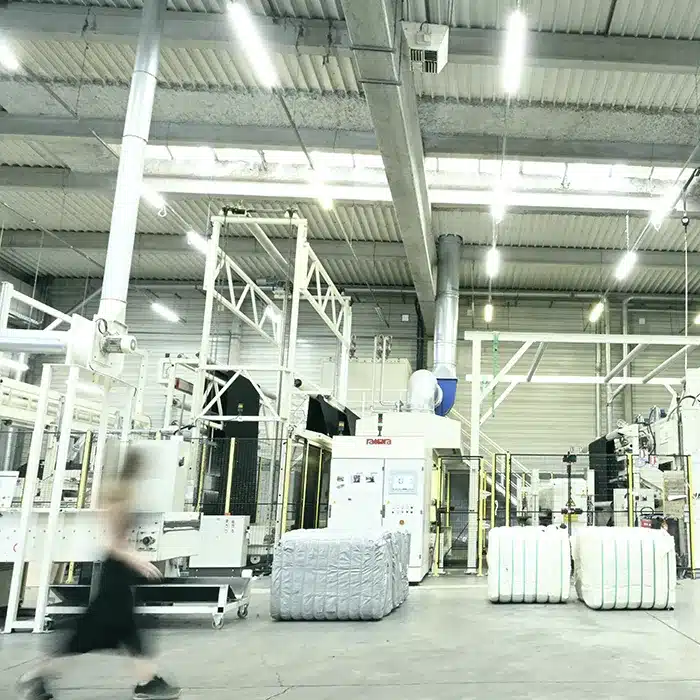